As vehicle owners, we constantly seek ways to protect our investment and keep our beloved rides pristine. Undercoating treatments are a popular method to shield our cars from the elements and corrosive substances. Ziebart, a renowned name in automotive protection, has been providing undercoating services for decades, garnering a loyal following. However, like any other product or service, Ziebart’s undercoating is not without its share of issues.
Common problems of Ziebart Undercoating are:
- Ineffectiveness over rusty metal
- Limited resistance to heavy abuse
- Development of cracks over time
- Drainage clogging due to improper application
- Reduced value for short-term ownership
- Moisture lock-in during application
- Rubberized undercoating can make it challenging for mechanics
- Require regular applications for ultimate protection
- It may not be compatible with certain types of materials
In this blog post, we’ll explain Ziebart’s undercoating problems in detail, from application concerns to potential long-term effects and possible solutions. We’ll examine customer experiences, weigh the pros and cons, and ultimately help you decide whether Ziebart’s undercoating services are the right choice for your vehicle.
Keep Reading!!
Ziebart Undercoating Problems & Solutions
1) Ziebart undercoating is less effective when applied over existing rust on a vehicle’s metal components.
Undercoating protects a vehicle’s undercarriage from corrosion, rust, and damage caused by exposure to moisture, salt, and other harsh elements. However, Ziebart undercoating may be less effective when applied over existing rust on a vehicle’s metal components.
Understanding why this happens and how to avoid potential issues is crucial.
Why is Ziebart undercoating ineffective over existing rust?
1) Adhesion Problems
When applied over existing rust, the undercoating may not adhere properly to the metal surface, reducing rust removal capabilities and corrosion.
Rust compromises the bond between the metal and undercoating, resulting in a weaker barrier that can quickly fail.
2) Rust Progression
Rust is a product of oxidation, where iron reacts with oxygen in the presence of moisture. If the ziebart undercoat is applied over rust, the oxidation process can continue underneath, causing the rust to spread and weaken the metal structure.
The undercoating does not halt the rusting process but merely covers it, which can lead to more significant problems in the long run.
3) Ineffective Sealing
The primary purpose of undercoating is to create a barrier between the metal and external elements. However, when applied over rust, the undercoating may not form a continuous, uniform layer, allowing moisture and other corrosive substances to penetrate the barrier and come into contact with the metal surface.
Solution
- Before applying Ziebart undercoating, removing any existing rust from the metal components is essential. This can be done using a wire brush, sandpaper, or a rust-removing chemical solution. After removing the rust, clean the surface thoroughly to ensure proper adhesion of the undercoating.
- After rust removal, prepare the surface by cleaning it with a degreaser or a metal cleaner. This step ensures the metal surface is free from contaminants, oils, or dirt that could interfere with the undercoating’s adhesion.
- Apply a rust-inhibiting primer to the cleaned, rust-free metal surface. The primer acts as an additional protection against rust and improves the bond between the metal and the undercoating.
- Once the primer has dried, apply the Ziebart undercoating per the manufacturer’s instructions. Ensure that the undercoating is applied evenly and consistently, covering all the critical areas of the undercarriage.
2) It may not withstand extreme conditions or heavy abuse.
While Ziebart is designed to provide a layer of protection, there are limitations to its effectiveness, particularly when subjected to extreme conditions or heavy abuse, such as off-roading or exposure to severe chemicals.
Why Ziebart undercoating may not withstand extreme conditions or heavy abuse:
1) Material Durability
Ziebart undercoating consists of a mixture of resins, waxes, and corrosion inhibitors that form a protective barrier over the metal surface. While it is designed to be durable and resilient, it may not withstand the mechanical stresses and wear caused by off-roading or other extreme driving conditions.
Constant impacts, vibrations, and abrasion can weaken the undercoating, reducing its ability to shield the metal from the elements.
2) Chemical Resistance
This undercoating product is designed to protect against common environmental factors such as moisture and road salt. However, exposure to harsh chemicals, like strong acids, solvents, or industrial-grade cleaning agents, can compromise the undercoating’s integrity.
These chemicals may cause the undercoating to break down, lose its adhesion, or become less effective as a protective barrier.
3) Temperature Fluctuations
Extreme temperature fluctuations can affect the performance of Ziebart undercoating. High temperatures can cause the undercoating to soften or become more susceptible to mechanical wear, while shallow temperatures can make it brittle and prone to cracking.
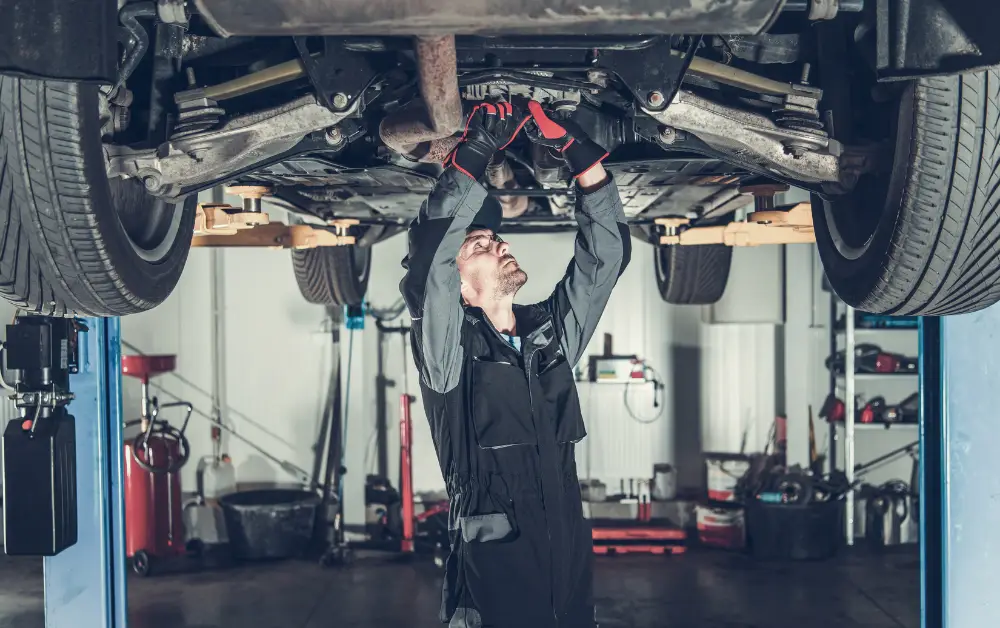
Solution
- If your vehicle is regularly subjected to extreme conditions or heavy abuse, consider using a heavy-duty undercoating explicitly designed for such scenarios.
- Regularly inspect the undercoating for signs of wear, damage, or degradation and address any issues promptly. Reapply the undercoating as necessary to maintain its effectiveness and ensure optimal protection.
- After exposure to harsh chemicals or heavy abuse, thoroughly clean your vehicle’s undercarriage to remove any residual substances that could affect the undercoating’s performance.
- If possible, avoid exposing your vehicle to extreme conditions or heavy abuse that could compromise the effectiveness of the undercoating.
You May Also Like To Read:
3) Ziebart undercoating may develop cracks Overtime.
Ziebart undercoating is designed to shield a vehicle’s undercarriage. However, the undercoating may develop cracks over time, compromising its effectiveness as a protective barrier.
Causes of Ziebart undercoating cracks
1) Aging
As the undercoating ages, it can become more susceptible to cracking. The materials used in the undercoating, such as waxes and resins, may break down over time, losing their elasticity and becoming more brittle.
2) Temperature Fluctuations
Extreme temperature changes can cause the undercoating to expand and contract, resulting in cracking. High temperatures can soften the undercoating, while shallow temperatures can make it more brittle.
3) Mechanical Stress
The undercoating may be subjected to mechanical stress from daily driving, impacts from rocks or debris, and vibration. Over time, this stress can lead to the formation of cracks in the undercoating.
4) Improper Application
If the undercoating is applied too thickly or unevenly, it may be more prone to cracking. The thicker areas may not dry or cure properly, leading to a weaker bond with the metal surface.
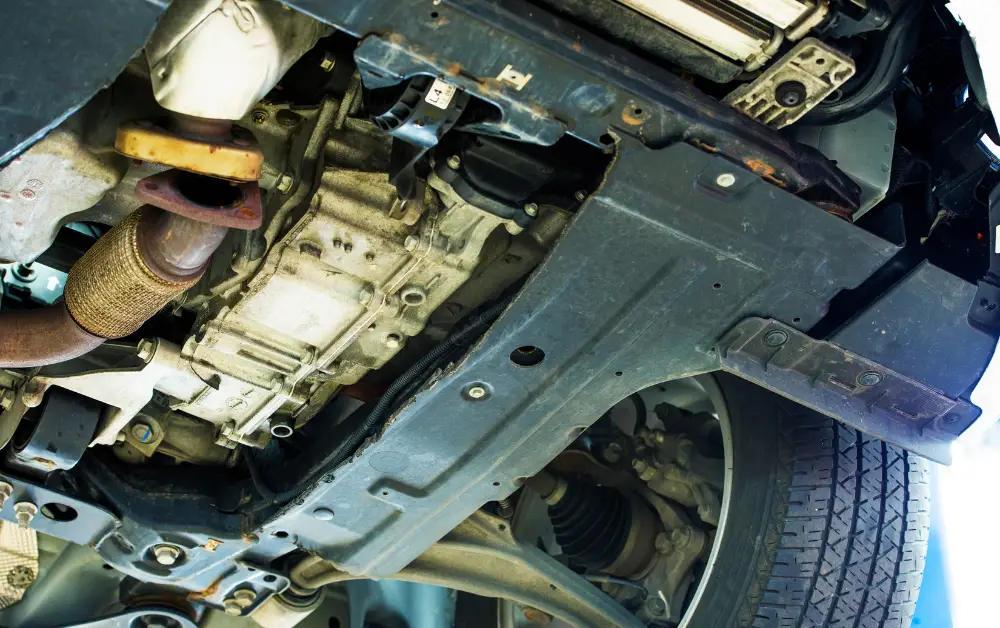
Solution
- Ensure the undercoating is applied correctly, following the manufacturer’s guidelines. This includes applying the undercoating evenly and at the recommended thickness to minimize the risk of cracking.
- Inspect the undercoating regularly for signs of cracks or damage. Please address any issues promptly by repairing or reapplying the undercoating as needed to maintain its effectiveness.
- If possible, limit your vehicle’s exposure to extreme temperature fluctuations, which can contribute to undercoating cracking. Park your vehicle in a garage or use a car cover to shield it from the elements.
- When touching up or reapplying the undercoating, ensure that you use premium undercoating brands that adhere well to the existing undercoating. Incompatible products may not bond properly, leading to additional cracking and reduced protection.
4) It may trap moisture, potentially accelerating the corrosion process.
If the undercoating is applied when there is already moisture on the vehicle’s surface, it can trap the moisture and potentially accelerate the corrosion process.
Implications of moisture trapping in Ziebart undercoating
1) Accelerated corrosion
Trapped moisture creates an environment conducive to corrosion. When moisture is in direct contact with the metal surface, it reacts with the metal, leading to oxidation and the formation of rust underneath. If the undercoating traps moisture, it can promote corrosion instead of preventing it.
2) Compromised Adhesion
Moisture on the metal surface can negatively affect the bond between the undercoating and the vehicle’s undercarriage. The undercoating may not adhere properly, leading to a weaker barrier that is less effective in rust protection and corrosion.
3) Formation of Blisters
When moisture is trapped beneath the undercoating, it can cause blisters or bubbles in the coating layer. These blisters can weaken the integrity of the undercoating, making it more susceptible to cracking, peeling, or flaking.
Solution
- Before applying the undercoating, thoroughly clean the vehicle’s undercarriage to remove any dirt, grease, or contaminants. This ensures that the undercoating can adhere properly to the metal surface.
- After cleaning the undercarriage, ensure it is scorched before applying the undercoating. Use a clean, dry cloth or an air blower to remove any remaining moisture.
- Apply the undercoating in a dry and well-ventilated area, away from direct sunlight or extreme temperatures. This helps to ensure that the surface remains dry during the application process and that the undercoating dries and cures properly.
- Follow the manufacturer’s instructions or hire professional undercoating service provider for applying the Ziebart undercoating, paying particular attention to the recommended thickness, drying time, and additional preparation steps.
- After it has dried, inspect it for any signs of moisture trapping, such as blisters or bubbles. If any issues are detected, address them promptly by removing the affected undercoating, drying the surface, and reapplying the undercoating as needed.
5) When not applied correctly, Ziebart undercoating can clog a vehicle’s drainage system.
When not applied correctly, Ziebart coating can clog a vehicle’s drainage systems, leading to water accumulation and an increased risk of rust.
Consequences of drainage clogging caused by improper Ziebart undercoating application:
1) Water Accumulation
When the undercoating clogs a vehicle’s drainage systems, it can obstruct the water flow, accumulating in various undercarriage areas. This creates a favorable environment for rust and corrosion, as the trapped water promotes oxidation.
2) Premature Rust Formation
The increased moisture exposure caused by clogged drainage systems can accelerate the formation of rust on the vehicle’s metal components. This can lead to structural issues and reduce the overall lifespan of the vehicle.
3) Increased Maintenance Costs
Clogged drainage systems may require additional maintenance to clear the blockages and repair any damage caused by the trapped moisture. This can result in increased costs and time spent on vehicle upkeep.
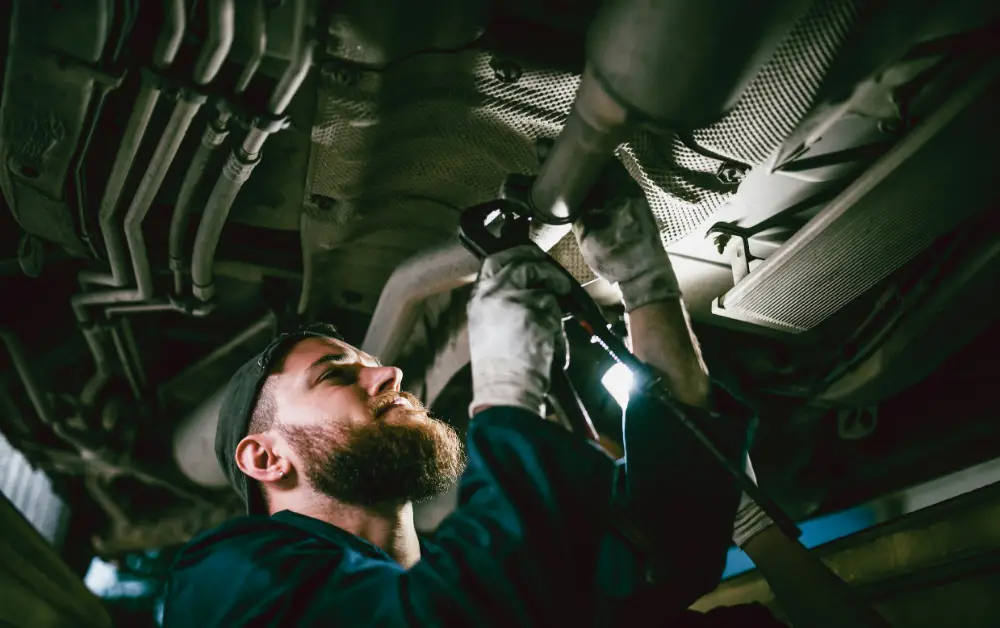
Solution
- Before applying the undercoating, take the time to identify and understand the locations of your vehicle’s drainage systems.
- Follow the manufacturer’s instructions for applying the Ziebart undercoating, paying particular attention to the recommended thickness and additional preparation steps.
- Ensure that the undercoating is applied evenly and consistently, avoiding the drainage systems to prevent clogging.
- When applying the undercoating, use masking tape or protective covers to shield the drainage systems from the undercoating material.
- Inspect your vehicle’s drainage systems regularly for any signs of clogging or obstruction. If you notice any issues, address them promptly by clearing the blockages and ensuring the systems function correctly.
- If you are unsure about applying the undercoating yourself or are concerned about potentially clogging the drainage systems, consider seeking the assistance of a professional automotive technician.
6) Ziebart undercoating must be applied regularly for Ultimate Protection
Ziebart undercoating is designed to provide a protective barrier adding rust removal capabilities, corrosion, and damage to a vehicle’s undercarriage. However, undercoating must be applied regularly to maintain optimal protection, which can be time-consuming and expensive for vehicle owners.
Challenges associated with regular Ziebart undercoating applications:
1) Time Consuming
Regularly applying the undercoating can be a time-consuming process, as it requires proper surface preparation, application, and drying time.
Vehicle owners with busy schedules may struggle to allocate the necessary time for this maintenance task.
2) Costly
The cost of the undercoating material and any labor costs associated with the professional application can add up over time.
For vehicle owners on a tight budget, the expense of regular undercoating applications may be a significant consideration.
3) Inconsistent Application Quality
If the vehicle owner or different technicians apply the undercoating over time, the quality and consistency of the application may vary.
This can lead to uneven protection and potentially compromise the effectiveness of the undercoating.
Solution
- To ensure you do not overlook the need for regular undercoating applications, set up reminders in your calendar or use a vehicle maintenance app to help you stay on top of this crucial task.
- If you are concerned about the quality and consistency of your undercoating applications, consider enlisting the help of a professional automotive technician. They can ensure that the undercoating is applied correctly and uniformly, providing optimal protection for your vehicle.
- Include the cost of regular undercoating applications in your vehicle maintenance budget. By planning for this expense, you can ensure you have the necessary funds available when reapplying for the undercoating.
7) Ziebart rubberized undercoating makes it challenging for mechanics to access and work on your car’s undercarriage.
Ziebart undercoating can make it challenging for mechanics to access and work on your car’s undercarriage, potentially leading to increased labor costs and time.
Challenges faced by mechanics due to rubberized undercoating:
1) Limited Access
Rubberized undercoating can create a thick, durable layer covering various undercarriage components. This layer can make it difficult for mechanics to access certain parts, such as bolts, fasteners, and connectors, which may be necessary for repairs or maintenance.
2) Difficulty In Removal
When mechanics need to access specific components or areas covered by the rubberized undercoating, they may need to remove the undercoating first.
The removal process can be time-consuming and labor-intensive, as the undercoating may adhere firmly to the metal surfaces.
3) Increased Labor Costs
Due to the challenges associated with accessing components and removing the rubberized undercoating, mechanics may need to spend more time working on your vehicle.
This increased labor time can translate into higher maintenance costs for the vehicle owner.
4) Potential For Incomplete Repairs
If the rubberized undercoating poses significant obstacles to accessing specific components, mechanics may be unable to perform comprehensive repairs or maintenance, potentially leading to ongoing issues with the vehicle.
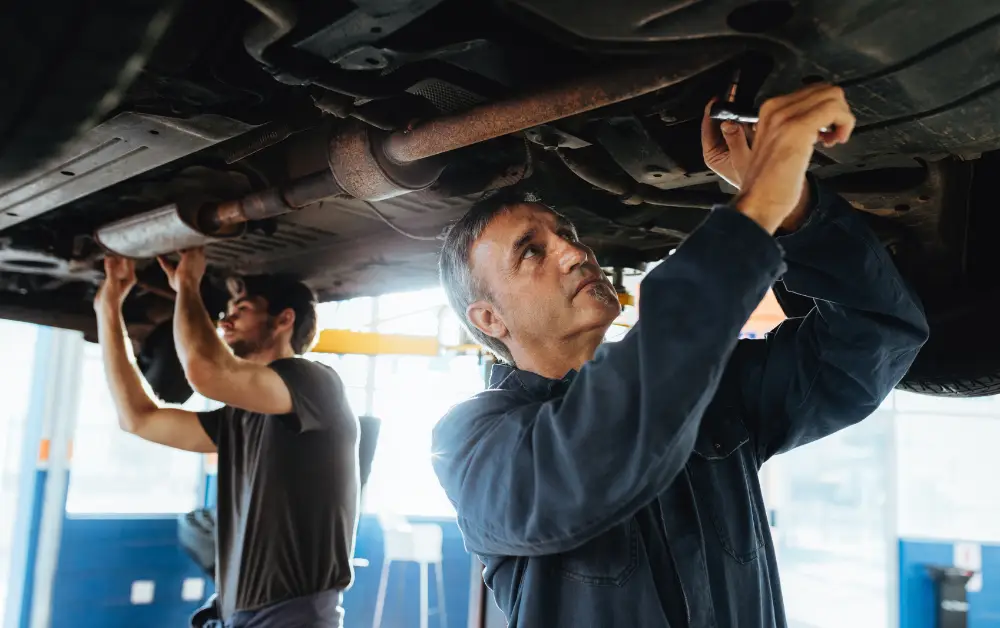
Solution
- Inform your mechanic about rubberized undercoating on your vehicle’s undercarriage. This can help them plan and prepare for additional time or resources to work on your vehicle effectively.
- When selecting a mechanic, opt for one with experience working with rubberized undercoating. They will be more familiar with the challenges and best practices associated with this undercarriage protection, potentially leading to more efficient and effective repairs.
- By conducting regular inspections of your vehicle’s undercarriage, you can identify and address any issues before they become more severe. This proactive approach can help minimize the need for extensive repairs and reduce the impact of rubberized undercoating on maintenance efforts.
8) Ziebart undercoating may not be compatible with certain types of vehicles or materials.
Ziebart is a well-known brand that offers undercoating services and products designed to help extend the life of a vehicle and maintain its structural integrity. However, compatibility issues may arise, necessitating a thorough vehicle assessment and consultation with a professional before proceeding with the undercoating process.
Common Issues
1) Material Compatibility
Vehicles are constructed using various materials, including metals, plastics, and composites. These materials can have different chemical properties and reactions to undercoating products.
The formulation of Ziebart undercoating may not be compatible with all materials used in a vehicle’s construction, potentially leading to adverse effects such as discoloration, weakening, or accelerated corrosion.
2) Vehicle Design and Specifications
Some vehicles have specific design features, such as unique suspension systems, exhaust configurations, or electronic components, that could be affected by the undercoating process. In these cases, applying Ziebart undercoating may not be suitable due to the potential risk of damaging these components or interfering with their proper functioning.
3) Manufacturer Recommendations
Vehicle manufacturers may have specific recommendations or requirements regarding undercoating, particularly for vehicles still under warranty. Applying an undercoating product not approved by the manufacturer could void the warranty or create complications during servicing or repairs.
Solution
Before applying any car undercoating product, it is crucial to ensure that it is compatible with all materials used in your vehicle’s construction. Choosing a product that suits the various materials in your car’s undercarriage is essential to guarantee the best possible protection.
9) This can incur additional costs for vehicle owners.
While the undercoating offers numerous benefits, it can also lead to additional costs for vehicle owners if it requires repair or removal due to damage or improper application. In this article, we’ll discuss the financial implications of Ziebart’s undercoating maintenance and repairs and strategies for minimizing these expenses.
Financial implications of Ziebart undercoating repair or removal:
1) Repair Costs
If the undercoating is damaged, cracked, or peeling, it may need to be repaired to maintain its protective capabilities. Repairing the undercoating can involve removing the damaged sections, cleaning and treating any underlying rust or corrosion, and reapplying the undercoating.
This process can be time-consuming and may require the services of a professional automotive technician, adding to the overall cost.
2) Removal Costs
In cases where the undercoating was improperly applied or if significant rust or corrosion is detected beneath the undercoating, it may need to be removed entirely.
The removal process can be labor-intensive, involving specialized tools and chemicals to strip the undercoating from the vehicle’s undercarriage.
This can result in additional labor costs and expenses related to the purchase or rental of the necessary equipment.
3) Reapplication costs
After repairing or removing the undercoating, it will likely need to be reapplied to restore the protective barrier. This can incur further costs related to the purchase of the undercoating material and the labor associated with its application.
Solution
- Ensuring that the undercoating is applied correctly from the beginning can help prevent damage and the need for costly repairs or removal. Follow the manufacturer’s instructions for application, or seek the assistance of a professional automotive technician to ensure a consistent, high-quality application.
- Perform regular inspections of the undercoating to identify any signs of damage or wear. Address minor issues promptly to prevent them from escalating into more significant problems that require expensive repairs or removal.
- Take preventive measures to reduce the likelihood of damage to the undercoating. For example, avoid exposing your vehicle to harsh chemicals or driving in conditions that may cause excessive wear on the undercoating, such as off-roading or driving on heavily salted roads during the winter.
FAQ
How Long Does Ziebart Take to Dry?
The drying and curing process might take longer for rustproofing and undercoating services, such as Ziebart’s Diamond Gloss or Ceramic Z-Gloss. The initial cure can take up to 12-24 hours, and the complete cure may take up to 24-48 hours, depending on the product and environmental conditions.
It’s generally recommended to wait at least 24 hours before driving in wet or dirty conditions to ensure the treatment has thoroughly dried and cured.
How Long Does Ziebart Last?
The Ziebart coating generally lasts approximately one year and cannot be considered a long-term solution for preventing corrosion.
Does Ziebart Only Work on New Cars?
Ziebart services are not limited to new cars; they can be applied to new and used vehicles. However, the effectiveness of treatments like rustproofing and undercoating may vary depending on the car’s condition
Affiliate Disclosure: Cars Escort is a participant in the Amazon Services LLC Associates Program. As an Amazon Associate, we earn from qualifying purchases made through affiliate links on our site. Read Our Disclaimer .